September. In Réunion Island, the sugar campaign is at its height. Every day, thousands of tonnes of sugar cane are delivered to the Bois-Rouge plant where they are milled, fibres are removed and the syrup is extracted.
The objective: to obtain sugar syrup and bagasse. The syrup is then concentrated to produce sugar crystals and molasses. These molasses are in the form of plant fibres that will be used as fuel in the Bois-Rouge power plant. The bagasse is transported between the two neighbouring sites on conveyor belts.
These belts, which are several dozen metres long, feed the plant continuously from Monday to Sunday morning. As a result, the bagasse directly enters the reception and storage building, where scraper shifts work day and night to ensure that the handling systems run smoothly. Wearing their personal protective equipment (PPE), they ensure that the quantities of bagasse received match the energy production requirements. In fact, one of them has just adjusted the bagasse level so that a smooth flow reaches the boilers.
The storage shed can hold up to 1,000 tonnes of bagasse. It contains several conveyor belts and the famous “scraper”, a machine that shapes the bagasse pile into a pyramid to optimise the feed into the boilers. This storage also reduces the risk of a blockage caused by too much bagasse leaving the belt.
If this happens, the operating team works to solve the problem as quickly as possible. They must act quickly! Their task is to unblock the plug formed by the mass of plant matter before it become harder than compressed wood and affects production. This type of incident may also be reported by the roundsman during his inspection patrols at the plant. The “eyes” of the team, he notices any malfunctions and reports them to the shift leader who, along with the operations manager, ensures the smooth operation of the systems.
The storage shed can hold up to 1,000 tonnes of bagasse. It contains the “scraper”, a machine that shapes the bagasse pile into a pyramid to optimise the feed into the boilers.
Although it is automated, the bagasse’s routing from the sugar factory to the boilers therefore requires constant care and is checked at every stage of the production process. With three turbines generating 100 MW of power, the Bois-Rouge plant provides nearly 25% of the island’s electricity. As this island is not connected to mainland power networks, the plant’s operation is crucial in ensuring that Réunion Island inhabitants have a stable electricity supply. A fact that the unit manager keeps in mind when he monitors the different systems from the control room. Let’s look more closely at what happens there…
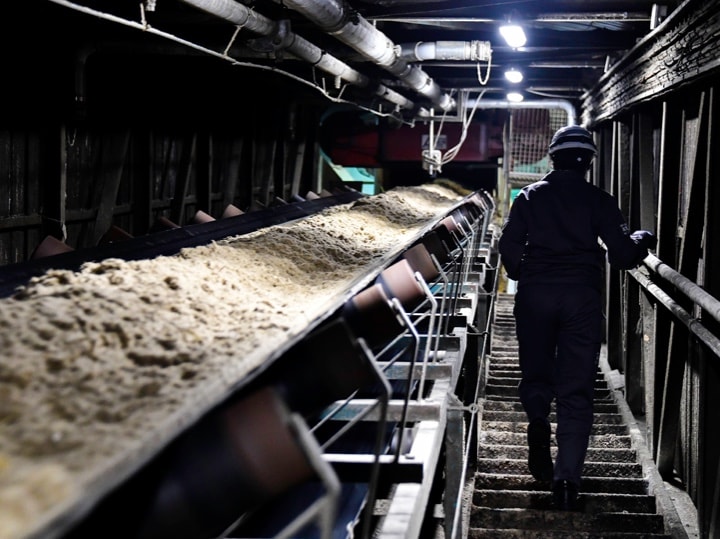
The operations team controls the transporting of the bagasse to the storage shed, where it is shaped into a pyramidal pile © Jérôme Boyer
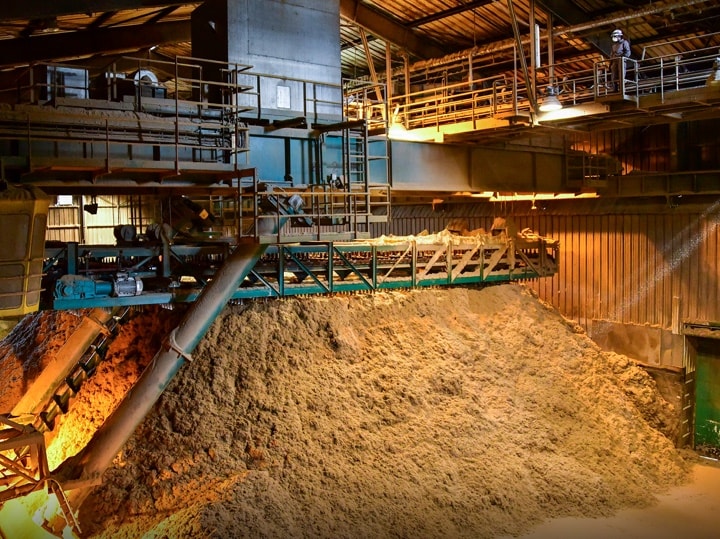
In the control room, the unit manager’s eyes are riveted on the monitoring screens. He analyses the information sent by sensors, takes readings and adjusts in real time combustion parameters such as the pressure and temperature of boilers. This pivotal role requires him to immediately respond to the unexpected. On the computer displaying the parameters of unit 1, a warning light has just lit up.
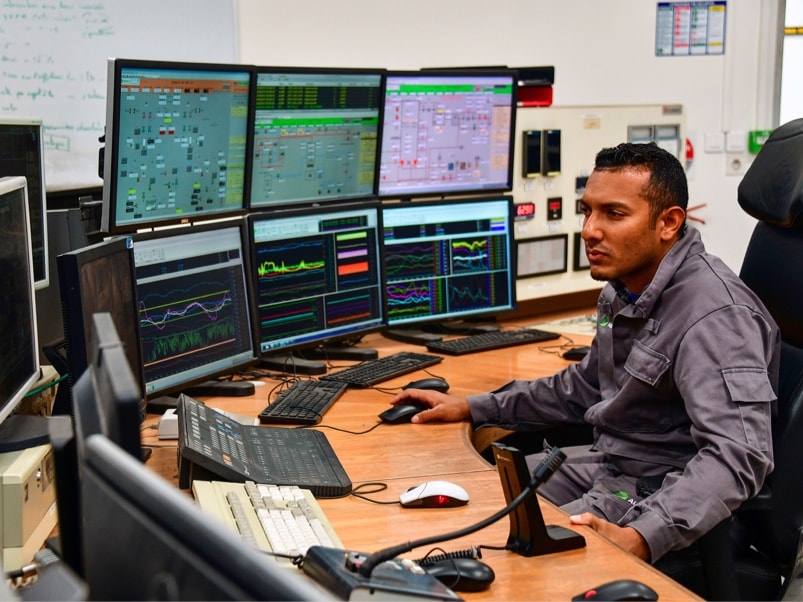
The unit manager monitors plant production from the control room © Jérôme Boyer
In a few seconds, the unit manager analyses the situation and takes corrective action to ensure the smooth operation of the systems. Depending on the information, he can also call on the shift leader and operations manager to decide together on the choices to make in order to ensure a stable supply to both the island’s power network and the sugar factory.
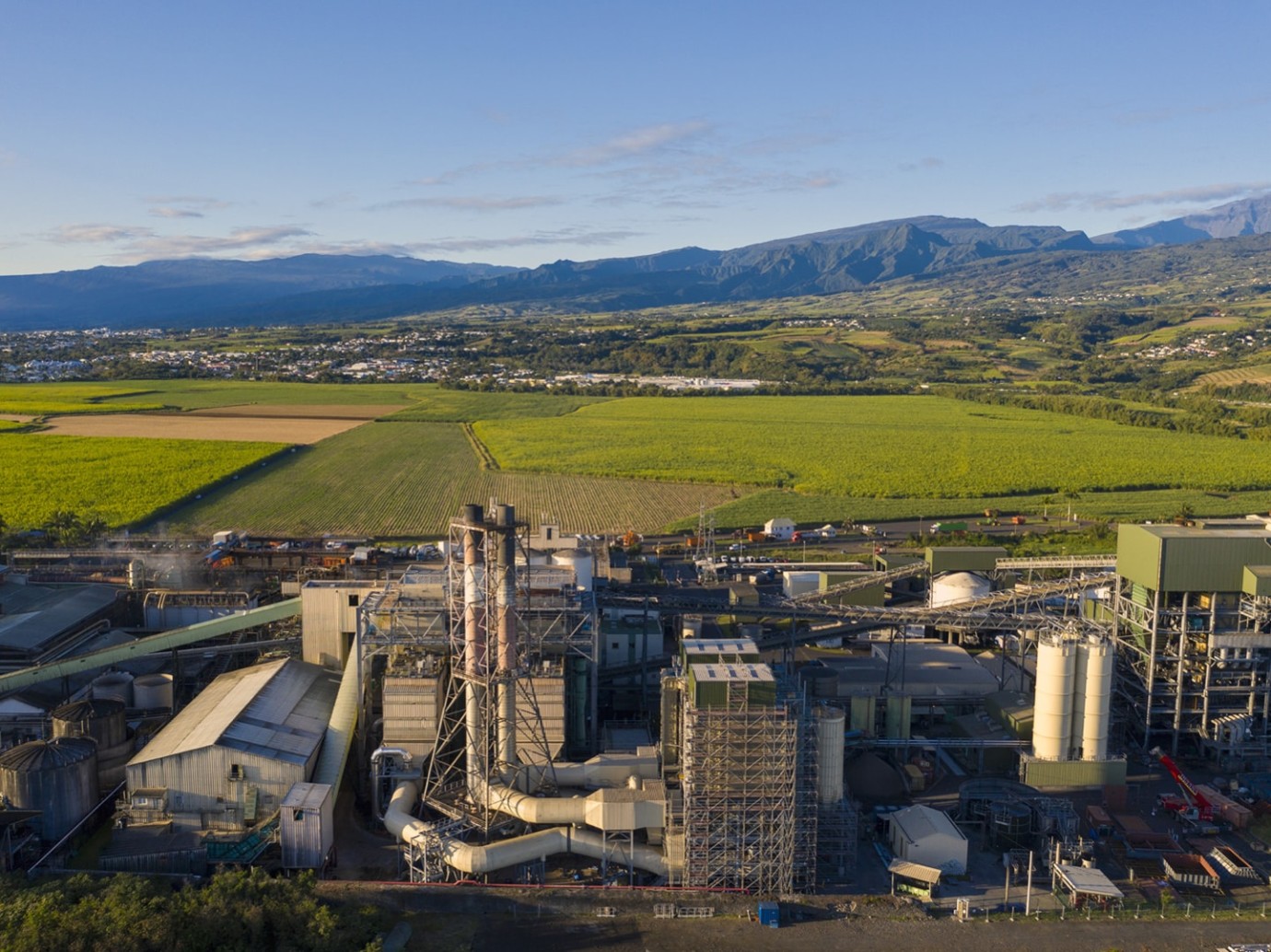
A panoramic view of the Bois-Rouge plant © Jérôme Boyer
On the ground, the unit manager can also count on the vigilance of the assistant controller and the thermal installation operator, who are responsible for optimising the steam production units. The thermal installation operator constantly monitors bagasse combustion, at 1200°C, through inspection holes into the furnaces. The heat produced is then sent to the boilers, which are also fed with demineralised water. The heat transforms the water into steam that drives a turbine connected to an alternator. The action of the turbine, which rotates at 6000 rpm, is then converted into an electric current that is sent to the Réunion Island power distribution network.
At the same time, the steam is condensed using a cold source (the air-cooling towers) for reuse in the boilers. As it flows in a closed circuit, purified water managed by the laboratory is used to prevent the risk of clogging and ensure the system’s operational longevity.
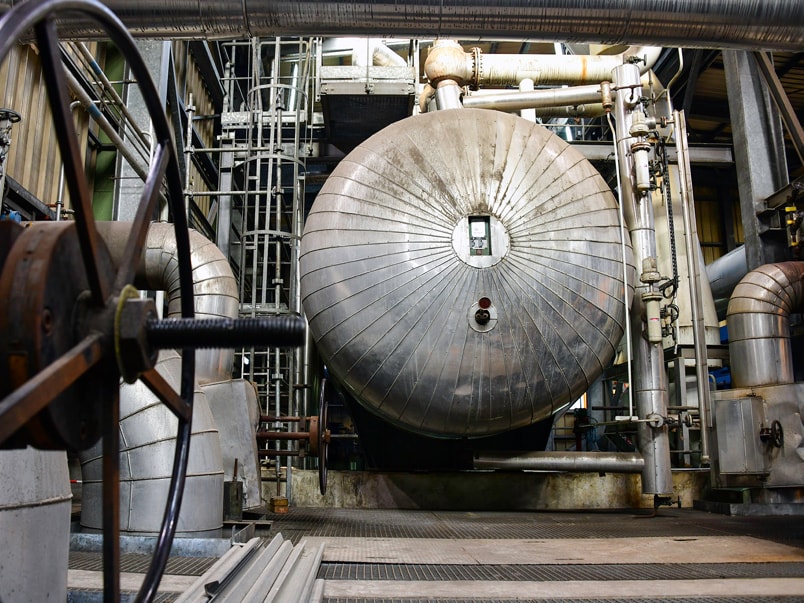
One of the water tanks, called the feedwater tank, in the Bois-Rouge plant © Jérôme Boyer
The work of the laboratory also includes performing chemical analyses on the processes and monitoring the quality of the water in the water-steam cycle and the cooling circuits. Environmental technicians are responsible for the plant’s flue gas treatment and water discharge treatment systems and check the quality of this waste entering the environment.
Monitoring and optimising the production process is therefore part of the daily work of the Bois-Rouge plant’s six operating teams as well as that of the maintenance department, which anticipates malfunctions, detects faults and handles the unexpected. Let’s go to meet them!
We are now with the plant’s maintenance team, whose role is to ensure the proper operation of the systems and, thereby, a smooth production process. As well as performing preventive maintenance, it can replace defective parts and fix any electrical or mechanical faults to repair equipment failures.
During the sugar campaign, the systems work very hard, like the bagasse conveyors which operate round the clock. The maintenance team acts immediately if there is a technical problem. If there is an emergency, such as a unit stoppage, it works as rapidly as possible to resume operation. It also does so at night, during public holidays and at weekends thanks to an on-call system. Usually, however, it becomes aware of problems during the Daily Operational Status Meeting (DOSM). This is attended by the site’s management, operation’s manager, shift leader and the heads of the maintenance and QSE departments to jointly set priorities.
In addition to remedial maintenance, the teams carry out scheduled work on the plant’s systems. This includes shaking down. It is carried out three times a week on boiler 3 to remove combustion residues with a high-pressure water jet. This is not the case today for the two technicians called to the site’s bagasse production unit to use the Robocop. This machine designed in-house replaces faulty shields, which are used to remove ash without halting boiler operation. On the way, they stop off at the warehouse, which contains no less than 13,000 items! The site’s island location means that the warehouse manager must always keep many parts in stock to ensure that the systems can rapidly resume operation in case of damage. There are even complete alternators in stock.
The Robocop machine was designed in-house. It replaces faulty boiler shields, which are used to remove ash without halting boiler operation.
We will end our visit on the administration department floor. This contains the offices of management, the accounting department, the human resources department and the QSE manager. With the help of all the employees, the QSE manager implements the plant’s Quality, Safety and Environment management system in accordance with the procedures and current regulations while also ensuring the well-being of everyone working there.
The day is ending and it is already time to say goodbye. Outside, the sun is slowly descending, colouring the Indian Ocean in orange shades. The evening breeze gently stirs the sugar-cane plantations. The night shift will arrive soon… At Bois-Rouge, production never stops!
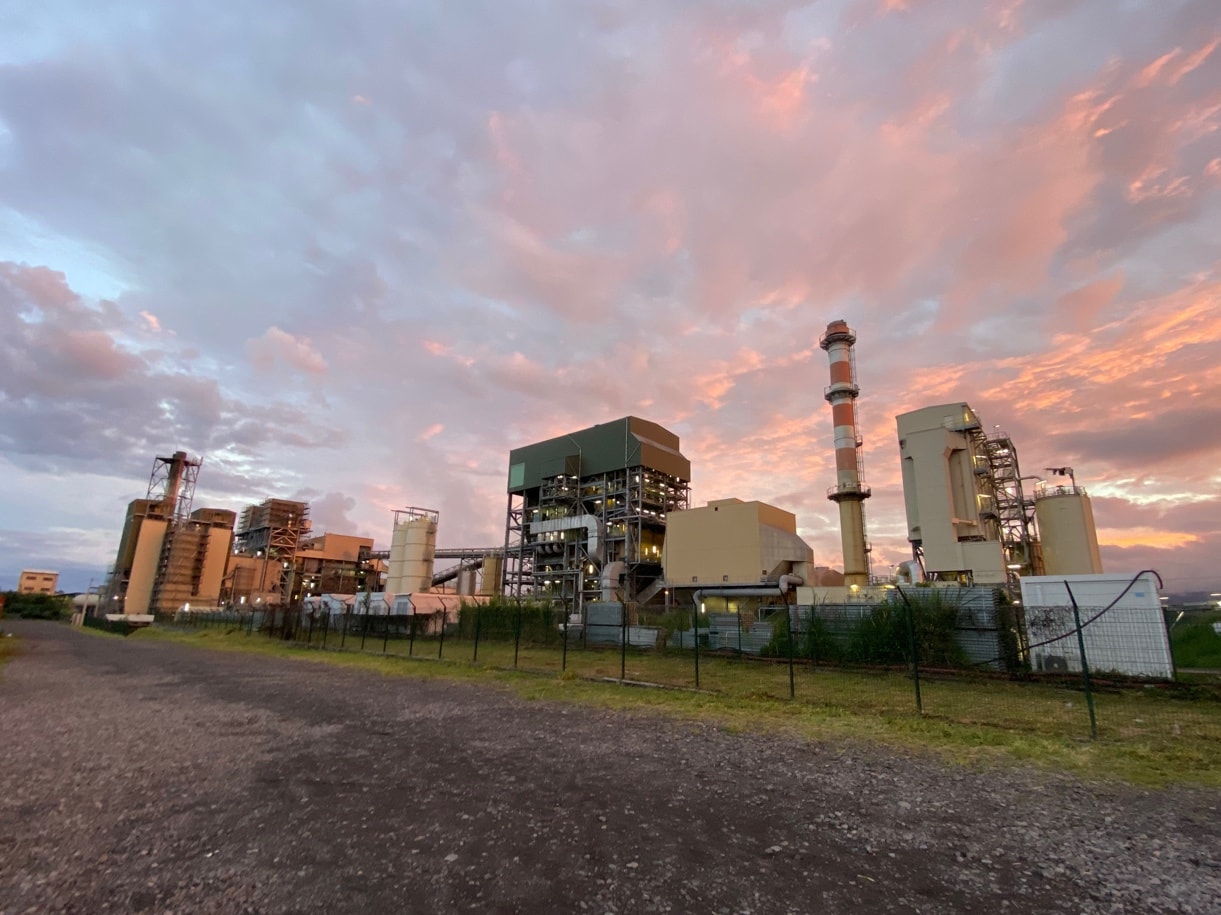
The Bois-Rouge plant at dusk © F. Caruzzi